Gear-obsessed editors choose every product we review. We may earn commission if you buy from a link. Why Trust Us?
Do you know a self feed bit from a drill tap? We’re here to help. Blade
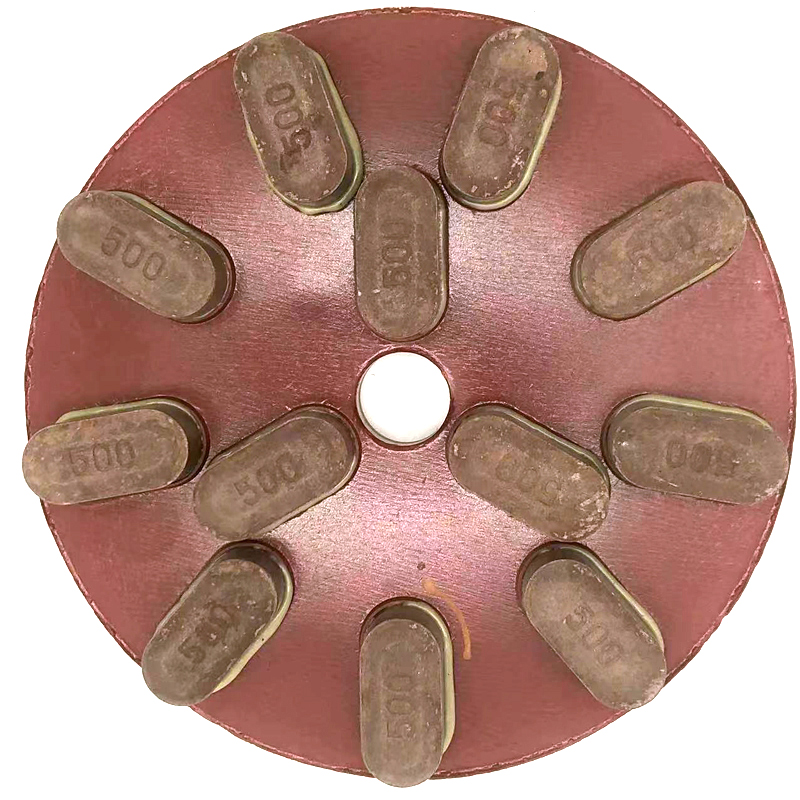
A hole is nothing. Or more precisely, it’s the absence of something—wood, metal, concrete, or any number of different materials.
Since holes are nothing, why do we care about them and how to make them? Well, even though they may be nothing out of something, it's important to know how to make a hole by using a drill bit quickly and accurately. And by accurately, I mean that you use the right drill bit for the job, and can put that hole right where you need it. The resulting hole should have a relatively smooth wall and be geometrically accurate, not oblong or oddly shaped.
We admit, the topic of hole making is somewhat confusing. There are a lot of ways to make the same hole using different drill bits. Sometimes, two or three different bits will do the same job with about the same speed and accuracy.
So it’s time to set the record straight. And I’m just the guy to do it. Since a hole is nothing, you might say that I’ve been making nothing for years—more than half a century. You might say that I’ve made a lot of nothing in my time and in every sort of material, too: plastic, wood, glass, tile, lumber, masonry, asphalt, soft steel, hard steel, stainless steel, aluminum.
I’m sort of a nothing expert. With a little coaching, you can be too.
Stick with me, it gets better from this point on. Really. There’s nothing to it.
This article will focus on the accessories to make a hole in the shape of a cylinder. The accessory that makes such a hole is a drill bit, in one form or another. We’ll go through these bits one at a time, to explain their use and benefits.
The cone-shaped tip of a twist drill bit cuts with a diagonal shearing action. The debris it produces is transported out of the hole by the helix-shaped channel machined into the side of the bit. The most commonly-available form of this drill bit is the type with a 135-degree tip. It’s designed for drilling metal, but it will also drill wood. There are forms of this drill bit that have a 118-degree tip that are more well suited for drilling wood, but in the last several years, these have become very hard to find (they have been displaced by the next bit shown, the brad point).
Industrial-duty versions of twist drill bits are made from various forms of high-speed steel (such as a cobalt-molybdenum alloy, M42), and these bits may also have a wear-resistant nitride (or other) coating that gives them a black or gold color. These heavy-duty bits better resist heat and wear when drilling metals, particularly thick pieces of steel, cast iron or stainless steel.
The tip of the bit is a sharp cone that cuts with a reaming action. Two adjacent spurs on the bit’s circumference scribe a sharp hole. The result is a carving action that produces a clean hole and relatively smooth wood chips that are readily ejected by the bit’s helix shape.
A screw needs to be driven into the center of a hinge hole because, if it’s not centered, the first screw driven will pull the hinge out of position. Another problem that occurs from an off-center screw is that the screw's head will hit the hinge as it's driven, rather than being able to be driven fully home. That’s where these specialized bits come in. Their housing has a cone-shaped tip that seats in the center of the hinge hole. The drill bit inside the housing is, therefore, centered in the hinge hole, providing a perfect pilot hole for the hinge screw. When you press down on this accessory, the spring-loaded bit emerges from the housing and drills the hole.
Wood screws come in all shapes and sizes today, but if you want to drive a traditionally shaped version of this fastener, particularly into a hole topped by a wood plug, then the easiest way to do that is to drill a tapered hole, specifically shaped for traditional wood screws. This tapered bit has a countersink at the top, a reamer that cuts away a cavity that allows a wood plug to be seated above the screw. You can skip the wood plug, if you choose.
This is among the dead simplest of all hole makers. It’s a steel rod that’s been forged flat with cutting edges ground on its lead edge. Although it comes in many variations, there are two basic types, those with a lead screw that pull the bit through the wood and the one shown, without the lead screw (you push). One of its most common uses is for making through holes (in one side and out the other) in framing lumber so that something else may pass through, such as a bolt, pipe, or cable.
The self-feed type is an extremely aggressive and rugged large-diameter bit preferred by plumbers for blasting out holes in house framing. The smallest is typically somewhere around 1-3/8 inches and the largest is around 4-5/8 inches. Plumbers and HVAC contractors prefer these bits for making big holes for pipes. The lead screw pulls the bit through the lumber extremely quickly as the gigantic saw-like teeth cut the hole perimeter. A sweeping chisel-like cutter clears the wood within the bit’s circumference. The bits diameter is so large and the torque required to turn them is so great, that they are typically used with a specialized hole-making power tool called a joist drill. With its head and chuck at a right angle to the drill body, it can squeeze in between floor joists and studs to quickly knock out holes for pipe.
These are the long wood-boring twist bits used by carpenters and electricians, primarily, for making holes in framing for passing wire and bolts. A ship auger has a lead screw at its tip that pulls the bit through the wood, and the bit’s body is shaped like a spring. This design creates a hollow center that allows a massive flow of wood chips through the bit as it turns. Furthermore, the bit’s cutting edge acts like a chisel that turns horizontally. Some of these bits are an extra-rugged type that can cut through nails that the bit is likely to encounter on its hole-boring journey.
Although this bit appears superficially like the self-feed bit shown above, it's a hole maker used for fine work, such as in building free-standing furniture, wall-hung cabinets, and chairs. It's used particularly where large-diameter hole with a smooth wall is called for. For example, in chair making where a turned leg is inserted into a chair seat. It's also used where you need to make a number of overlapping flat-bottomed holes for clearing the bulk of wood out of a cavity. Forstners come in a range of sizes, from 1/4 inch to those slightly larger than 2 inches.
This accessory saws a hole in wood, composites, and even sheet metal. It’s guided by a drill bit mounted in a mandrel that helps the saw find its center. In this respect, the hole saw is not a drill bit at all. Rather, it saws out a circular plug of wood (or other material) that must be removed after the cut is complete. It’s a simple and rugged accessory that works well for making door knob and dead bolt holes in doors and for work that requires an accurate, smooth-walled hole, particularly where that hole is large diameter. Although hole saws are deep enough to make a hole through framing lumber, it’s not their strong suit. They are comparatively slow cutting compared to many drill bits of the same diameter. For large holes through framing lumber, use a self-feed bit, ship auger or even a large-diameter spade bit.
Developed in the 1970s as the Unibit by inventor Harry C. Oakes, this accessory is perfect for electricians and metal workers to carry in their tool box because one bit makes a range of holes in sheet metal and metal plate. Each step in the bit is a different diameter. These bits come in a variety of sizes and configurations and with various finishes that range from plane polished steel to titanium nitride coated. Because these bits see a tremendous amount of strain, most are made out of high-speed steel.
For quickly making a threaded hole, nothing beats the drill tap. The tip is a drill bit; its back is a tap. The drill clears the hole, while the tap cuts thread in it. The most common form of this accessory is a kit of several of these bit sold together and sized to match holes for the machine screws used in electrical wiring.
Drilling through rock, concrete, concrete block, brick, and mortar requires a tough bit. Or rather, a tough bit with an even tougher tip, preferably a piece of carbide brazed onto the body of the bit. The bit itself has to be able to withstand bending or snapping and the carbide has to stay securely attached to it. But with a well-made masonry bit, that's exactly what you get–a tough bit with an ever tougher carbide tip.
These bits come in two basic forms. The general hex-shank masonry bit is for use in an ordinary drill driver. Its hex shank prevents the bit from slipping in the drill's chuck. The other form of this bit is designed for use in a specialized power tool called an SDS rotary hammer. This tool has a spring-loaded chuck that allows the bit to be inserted, it doesn't have to be tightened. SDS masonry bits have a specialized base formed to permit this easy insertion into the chuck of an SDS rotary hammer.
Woodworkers have been making holes since people began working with wood. A time-honored bit for making holes in wood is the auger bit. It's meant to be used in a tool called a bit brace (or sometimes, simply, a brace). These bits were available in various shapes, diameters and lengths . Until relatively recently, they were produced in a configuration much like the one you see here, a design hundreds of years old. The chief benefit of this bit is that it cuts consistently, if slowly compared to a bit used in a power tool. When its cutting lips are sharp, it makes a smooth, round, and straight hole in hardwood and softwood. And if it sticks (which it will occasionally in difficult grain, especially in hardwood), you just turn the brace in reverse for a couple of revolutions and then turn it forward again. Because millions of auger bits were made, you can still get good ones on eBay, at flea markets, and woodworking shows where there are antique tool vendors.
Drill points scoop out wood as they turn and can be used in a tool called a Yankee push drill. They can also be used with another low-speed analog hole drilling tool called an eggbeater drill (as its name implies, its powered by a geared hand crank like that found on an eggbeater).
Roy Berendsohn has worked for more than 25 years at Popular Mechanics, where he has written on carpentry, masonry, painting, plumbing, electrical, woodworking, blacksmithing, welding, lawn care, chainsaw use, and outdoor power equipment. When he’s not working on his own house, he volunteers with Sovereign Grace Church doing home repair for families in rural, suburban and urban locations throughout central and southern New Jersey.
The Right Way to Use a Fire Extinguisher
Can Your A/C Only Cool a Space by 20 Degrees?
J-B Weld: Just How Tough Is It?
Make Your Own Smoker Out of a 55-Gallon Barrel
Simple Fixes for Toilet Trouble
These Are the 3 Most Expensive Home Reno Projects
The Right Way to Prune a Tree
Are You Sure You Know How to Use a Screwdriver?
How Do Air Purifiers Work, Exactly?
Chopping Metal is Fun With a Cold Chisel
How to Kill Those Pesky Mosquitoes in Your Yard
A Part of Hearst Digital Media
We may earn commission from links on this page, but we only recommend products we back.

Diamond Cutting Disc ©2023 Hearst Magazine Media, Inc. All Rights Reserved.