Enhanced metallurgy can overcome chlorine pitting corrosion, crevice issues
As production platform operators face growing pressures to curtail the costs of expensive offshore projects, the industry is embracing new material innovations in order to overcome these challenges. Incoloy 825 Capillary Tubing
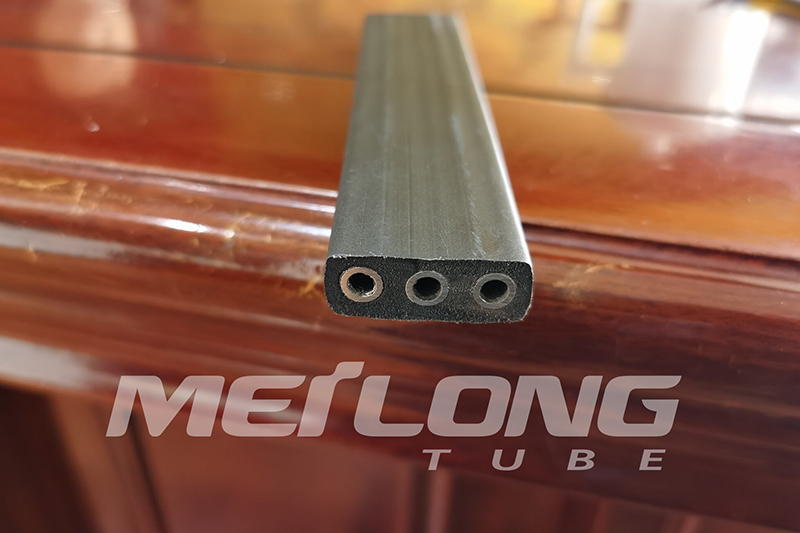
A key issue is failure caused by severe corrosion in the types of conventional stainless steels used for critical components such as hydraulic and instrumentation (H&I) tubing and chemical injection lines. With a possible solution being to improve the metallurgy of key components, the goal here is to examine how operators are upgrading to more advanced stainless steels. Through innovation, materials are evolving to yield superior performances, improved corrosion resistance, and better overall production economy.
Operators typically opt for conventional materials, such as carbon steels, 304L, and 316L grade stainless steels, in H&I systems and chemical lines due to low cost. However, these conventional grades do not justify the life cycle if there are severe corrosion issues.
The normal lifecycle of American Iron and Steel Institute (AISI) 316L steels in non-corrosive environments does justify the cost. Nevertheless, the same grade has exhibited a service life of less than five years in corrosive chloride-containing environments, or less than one year in some cases. Such failures will increase the costs of maintenance and down time and result in production losses that cannot be afforded by operators.
Higher contents of certain alloying elements within stainless steels can greatly improve their resistance to stress corrosion cracking (SCC); i.e. the introduction of nickel or ferrite into the metallic structure. Steels with an austenitic-ferritic metallurgy are found to be superior to conventional austenitic grades like 316 because they have higher mechanical strength and greater stability.
It is possible to gain a better understanding of how chemical composition affects a material’s resistance to corrosion phenomena, like SCC or pitting, by examining the pitting resistance equivalents (PRE) values of stainless steels. This number is widely accepted as the best method to rank this resistance.
PRE values are measured in accordance with exact testing procedures specified in the ASTM G48 standard. Generally, the higher the PRE number, the more corrosion resistant the steel. The formula used to calculate PRE takes into account the content of chromium (Cr), molybdenum (Mo) and nitrogen (N) within the steel’s metallurgy defined as, in weight: %PRE = % Cr + 3.3 %x Mo + 16 x % N.
The PRE values in the table show that AISI 304L and AISI 316L have a relatively low resistance to pitting. Austenitic ASTM 904L (UNS S08904) has a comparably high PRE number because it contains high levels of molybdenum and nickel. However, the limited market availability of these elements makes the grade more expensive, as is the case with 6% molybdenum, or 6Mo, steels which are chosen frequently for hydrogen sulfide (H2S) processes.
The highest PRE value is attributed to Sandvik SAF 2507 (UNS S32750), a high-alloy duplex steel, known as super-duplex due to its minimum PRE value of 42. The grade is characterized by its good chloride corrosion resistance combined with its high mechanical strength. These properties make it suitable for use in aggressive environments such as warm, chlorinated seawater and acidic, chloride-containing media.
In either offshore or shoreline installations, H&I tubes used to process oil or gas are typically subjected to high levels of salt, humidity, ultraviolet light, and temperature. This is especially true in environments where seawater is present and evaporates, leaving a higher concentration of chlorides on the tubing.
To more closely assess the corrosive effects of seawater on stainless steel tubes, Sandvik Materials Technology implemented a test installation on a platform in theGulf of Mexico that lasted 18 months.
Five grades were installed, including 316L (with a minimum 2.5% Mo). Also fitted was UNS NO8904, commonly known as 904L, a low carbon high alloy austenitic stainless steel in which the addition of copper gives it corrosion resistant properties which are superior to conventional chrome nickel stainless steels.
The other tested grades were: Sanicro 28 (UNS N08028), a high-alloy austenitic stainless steel designed for service in aggressive and corrosive environments; SAF 2205, a duplex (austenitic-ferritic) stainless steel characterized by high resistance to pitting, with a minimum PRE value of 35; and super-duplex SAF 2507. These materials were installed on the platform’s lower, or spider, deck where saltwater spray levels were high.
The tubes were subsequently exposed to an average temperature of 30°C (86°F) rising to a maximum of 42°C (107°F) over the 18-month test period. After the trial’s conclusion, the tubes were subjected to laboratory tests and analysis in order to assess their corrosion behavior.
A visual inspection revealed that the 316L tube was most corroded, particularly on the section that had faced seawards. Corrosion damage, discoloration and pitting were found. Sandvik SAF 2507 exhibited no signs of corrosion or pitting. Closer examination of the tubes with an optical microscope found crevice corrosion on the 316L and 904L tubes, but not on the super-duplex specimen.
The super-duplex SAF 2507 and AISI 316L grades were subjected to detailed analysis using energy dispersive x-ray spectroscopy (EDS) and also scanning electron microscopy (SEM). This exposed the presence of sulfur and chlorine in the corrosion area on the 316L tube sample.
The SEM/EDS scans revealed no visible signs of corrosion in the SAF 2507 tube sample, and they confirmed that no harmful corrosion agents were present after 18 months’ exposure in the Gulf of Mexico environment. In addition, no chlorine was present, only the original sulfur content of the material.
The Gulf of Mexico findings are highly relevant to companies seeking to upgrade their H&I or chemical injection tubing. The results show that super-duplex stainless steels offer an alternative to H&I tubing with superior corrosion resistance when the marine environment proves too severe for conventional materials.
The super-duplex material’s performance in seawater is comparable to highly alloyed austenitic stainless steels despite an overall lower content of costly constituents such as nickel and molybdenum. While it can be said that the performance requirements are addressed by 6Mo grades to some extent, those materials can be too expensive to be cost-effective.
The right choice of tube material, with an enhanced metallurgy, can be crucial in overcoming chlorine pitting corrosion and crevice issues with instrumentation, hydraulic systems, and chemical lines.
An 18-month test on the lower deck of a platform in the Gulf of Mexico shows that SAF 2507 is operationally reliable and longer service life in corrosive, chloridic environments where seawater is present as an alternative to carbon steels, 304L and 316L stainless steels, and 6Mo grades. The super-duplex is equipped to help operators improve their production economy, and can therefore reduce the costs of expensive offshore projects.

Encapsulated Hydraulic Control Line Barinder J S Ghai is the Regional Technical Marketing, EMEA at Sandvik Materials Technology based in Birmingham, UK. With more than 20 years of industry experience, Ghai focuses on maintaining and developing the technical marketing organization within the region to extend the technical and application knowledge on a regional and global level. He is a member of NACE, Eurocorr, SS World, MTI Europe and in 2016, presented and supported papers at several global conferences, including SS World and International Refining and Petrochemical Conference Abu Dhabi.